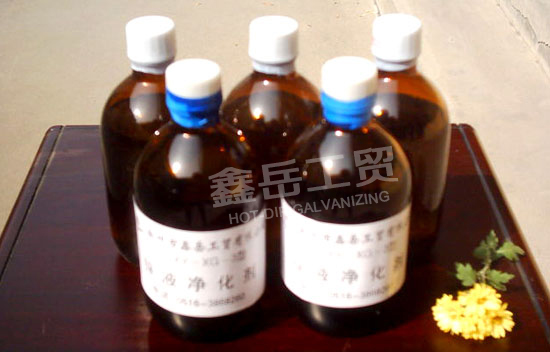
Design and Construct Hot Dip Galvanizing Plants both Domestically and Internationally
Add: Jinshan Bridge Zone, Xuzhou, Jiangsu, China
Mobile: 86-13805211808
Tel: 86-516-83168088
Email: xy-rjd@163.com
In the light of the high iron and impurity contents in molten zinc, poor fluidness and particles and fold on workpiece often occurred in hot galvanizing plants, our company has organized the famous specialists and scientific and technological personnel in many disciplines at home developed XY-XG-3 type purifying agent for molten zinc, a high and new technical product. It has effectively solved the difficult problem and filled in the gap in this field at home. Through testing and using, the agent reached the anticipated results and is well received by customers. At present the product is applying for a patent.
Notice
Do well pretreatment work, do not carry the harmful impurity into zinc pot, galvanizing agent needs the acid and iron eliminating, and it would be best if rinsing water for pretreatment could be fluid.
Because of the high volatility of the agent, No.2 operation should be quickly performed.
In order to avoid the splashing of molten zinc causing danger, operators should be well dressed in labor protection articles. Operation with caution and safety first.
Purifying Treatment Method of Molten Zinc:
Keep furnace temperature at 450℃-470℃.
Place dry thermal insulation bricks (with strong water absorption) into box with holes, quickly pour the purifying agent to them, insert the box into molten zinc and move it back and forth until boiling ends, and take out the box with holes.
Eliminate suspended substances on the surface of molten zinc; scatter ammonium chloride (1-1.5 kg/ m2) to further eliminate impurity on the surface.
Repeat the abovementioned steps three or four times.
Add the alloy, which is 0.5% of molten zinc, in uniform distribution way. After all the melting, repeat the abovementioned step once. (If there are excessive aluminum or other alloys in original molten zinc, the step-by-step method can be used)
The temperature is controlled at 430℃-440℃ and the standing time is 6-12 h (time is as long as possible).
When small workpiece is tested (the temperature is at 430℃ and dipping time is not changed), the surface and coating thickness is measured. If the coating is thick, the alloy, which is 0.1 % of molten zinc, can be added.
The zinc and the alloy can be added at one time until the alloy content in molten zinc reaches 1.5%.
After alloying is completed, the working temperature of molten zinc should be controlled at 440℃±5℃ and the lifting speed of traveling crane at 1.5 m / min.